Honda Probes Residual Stress Distribution in Complex 3D-Printed Automobile Structures
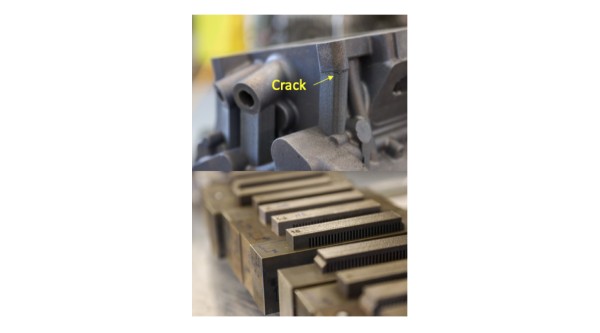
Scientific Achievement
Residual stresses in additively manufactured structures by different printing schemes were nondestructively measured by rapid neutron scanning.
Significance and Impact
Complex automobile structures are manufactured by additive manufacturing (3D printing) to reduce manufacturing costs for complex parts and improve fuel efficiency by reducing part weight. However, residual stress built-up from the manufacturing process can compromise the strength of complex structures or even result in cracking or fracturing. Neutron diffraction provides computation modeling validation for process optimization and mechanical integrity assurance.
Research Details
- Residual stresses were mapped in as-printed Al alloy mono cylinder engine block and multiple bench structures made with different processing parameters.
"Residual Stress Analysis for Additive Manufactured Large Automobile Parts by Using Neutron and Simulation,"
Tomohiro Ikeda, Satoshi Hirose, Hisao Uozumi, Ke An, Yan Chen, Alan Seid, Tatsuya Okayama, Takashi Katsurai,
SAE Technical Paper, 2020-01-1071, 2020, https://doi.org/10.4271/2020-01-1071.