Neutron Imaging Enables Optimized Annealing for Inconel Components Made by Additive Manufacturing
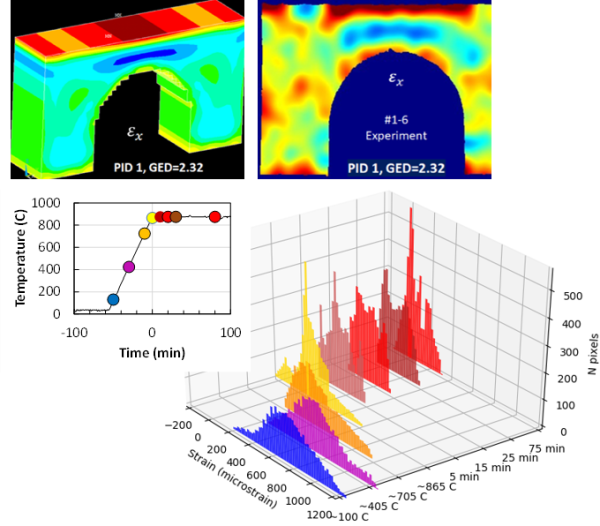
Scientific Achievement
Real-time monitoring of stress relaxation determines the optimal annealing temperature for additively manufactured (AM) Inconel 625 parts.
Significance and Impact
High temperature annealing of AM components to reduce residual stress is energy intensive and can lead to undesired secondary phases. Knowing the evolution of stress during annealing enables optimization of this process.
Research Details
- Strain evolution was measured at SNAP in wavelength-resolved 2D radiographs.
- Preliminary ex-situ studies were performed at NOBORU (J-PARC); the strain at selected locations was quantitatively measured at VULCAN.
- Predictions from a full electroplastic mechanical model agree with room temperature measurements
"Monitoring residual strain relaxation and preferred grain orientation of additively manufactured Inconel 625 by in-situ neutron imaging,“
Anton Tremsin, Yan Gao, Ade Makinde, Hassina Bilheux, Jean-Christophe Bilheux, Ke An, Takenao Shinohara, and Kenichi Oikaw,
Additive Manufacturing, 46, 102130 (2021).
DOI: https://doi.org/10.1016/j.addma.2021.102130