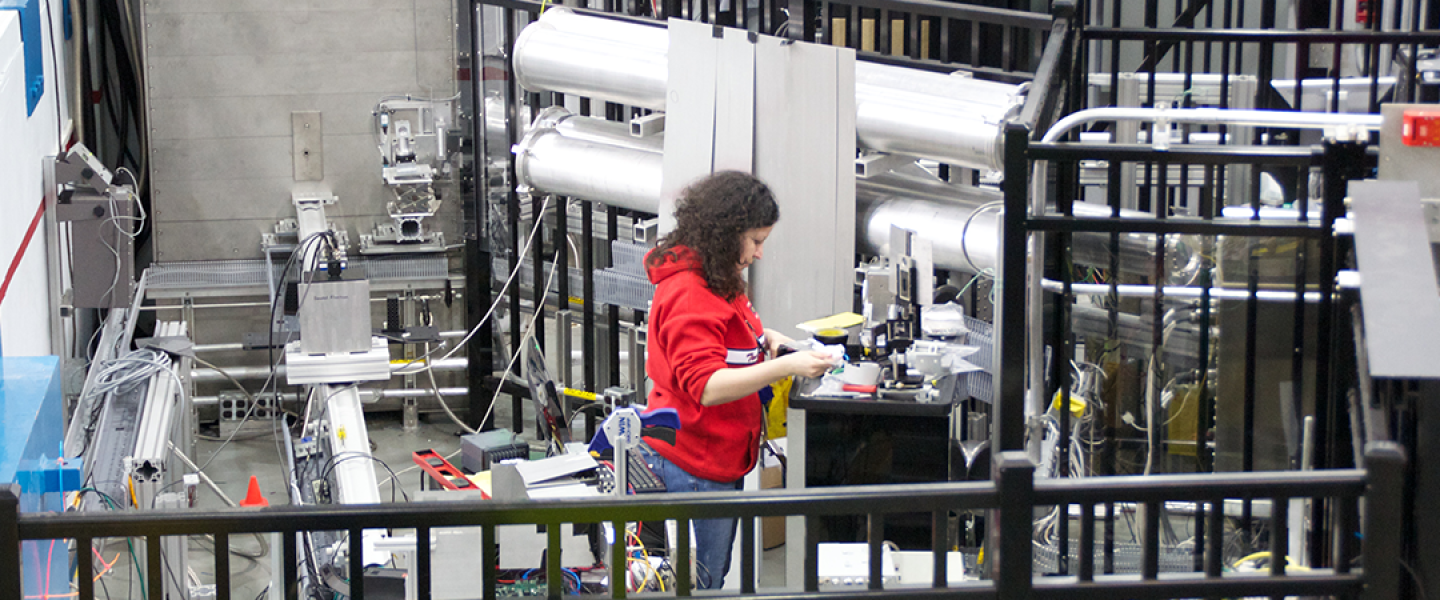
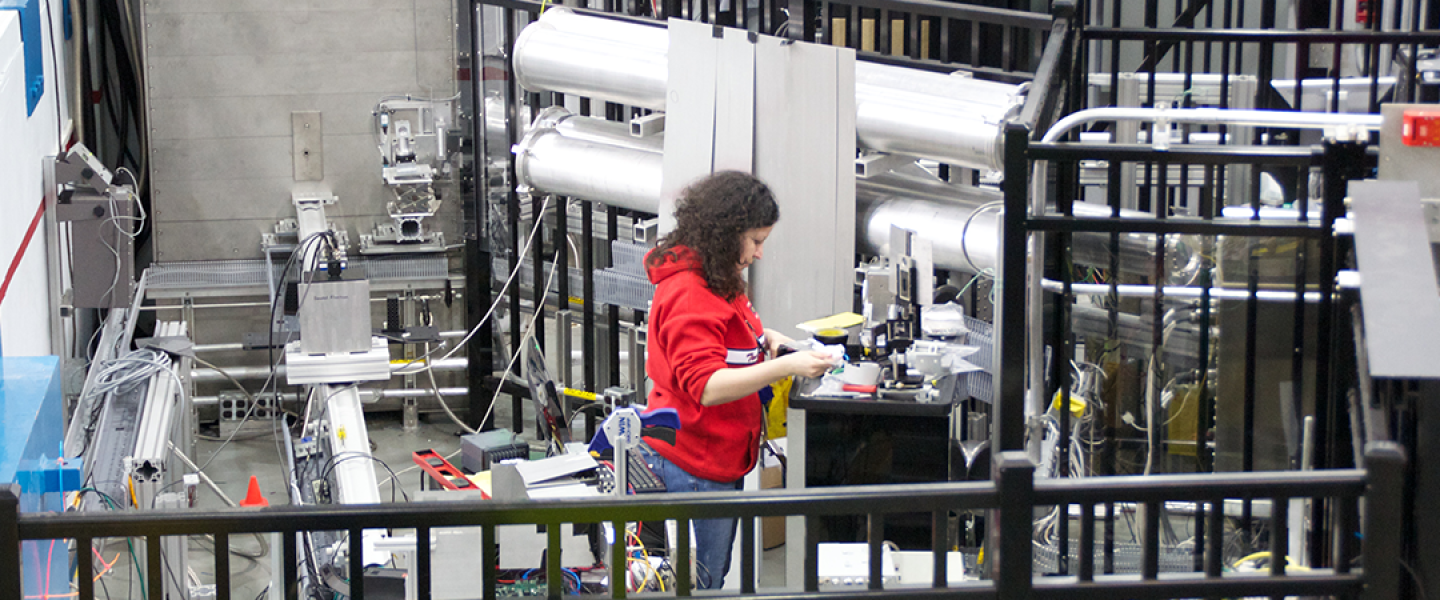
ORNL researchers were able to use neutron imaging (computed tomography or CT) to see inside of Inconel 718 turbine blades that were made using additive manufacturing, or 3D printing, to non-destructively study the internal structure of these blades, to model internal flow based on the imaged turbine and therefore improve the design of the blades. Anyone can look at the outside of a turbine blade, but imaging the internal structure without cutting the piece apart is very challenging. The interior surface roughness, as measured with neutrons, can be modeled to study/estimate the changes in air flow.
Nondestructive examination of complex additive manufactured components using neutrons is a valuable technique for imaging and measuring residual stress. Read more here.
Oak Ridge National Laboratory is managed by UT-Battelle LLC for the US Department of Energy